Automating equipment inspection and maintenance work, Hokkaido Electric Power, NTT Comware, and others conduct demonstration project HBA
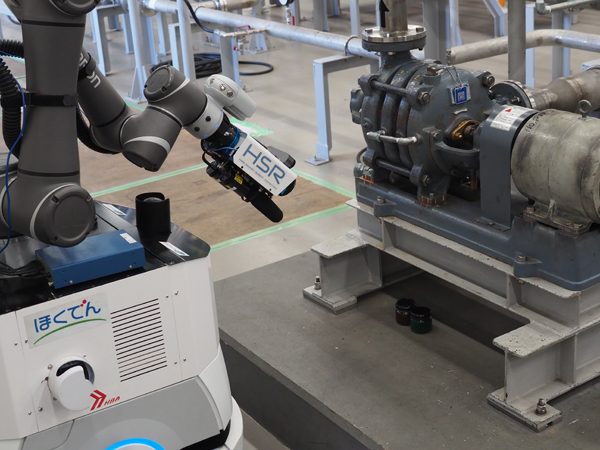
With HBA as the representative organization, seven parties including Hokkaido Electric Power Co., NTT Comware, Hokkaido University of Science, Hokkaido Research Organization, Hokkaido Telecommunications Network, and Interregion conducted a demonstration project inspection tour for the Ministry of Internal Affairs and Communications’ “Reiwa 6 Regional Digital Infrastructure Utilization Promotion Project” on Friday, the 28th of last month at the Thermal Power Technology Training Center of the Thermal Power Department on the premises of Hokkaido Electric Power Co., Inc.’s Tomato-atsuma Power Plant in Atsuma-cho, Hokkaido.
The Tomato-atsuma Power Plant is one of the largest thermal power plants in Hokkaido. Its total output is 1.65 million kW. It serves as the core power source for Hokkaido Electric Power.
This demonstration project aims to automate the inspection and maintenance work of equipment in the region, and alleviate the issues of labor shortages and technology transfer.
Specifically, the inspection and maintenance of equipment that was previously done by hand will be replaced by robots and digital technology.
Takanori Yamano, Managing Director of HBA, said, “Lack of human resources and transfer of technology are major social issues, and these issues are also becoming evident at power plants. If we can automate inspection and maintenance work at power plants, we can apply this to data centers and factories.”
During the tour, they demonstrated automated inspection of indoor equipment using robots and digital twins, automated inspection of outdoor equipment using robots, and automated weeding.
Shinji Fujiwara, Director of HBA’s Robotics Development Department, explained, “We are aiming for a CPS (cyber-physical system). We use AI and digital twins in cyberspace, and robots, drones, and IoT in physical space. By connecting cyber and physical with local 5G, we can handle the real and cyber worlds at the same time, and perform inspection and maintenance as if we were there, even from a remote location.”
For example, by using digital twins, it will be possible to centrally manage multiple power plants in Hokkaido from Sapporo.
Mitsuyuki Ono, Executive Officer of HBA, said, “We believe that the benefits of using digital space to operate facilities are quite large.”
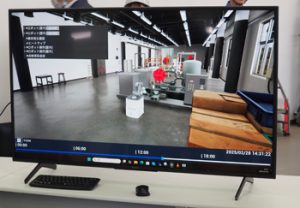
屋内遠隔操作デモ(デジタルツイン上でロボット操作)(Indoor remote control demo (operating a robot on a digital twin)
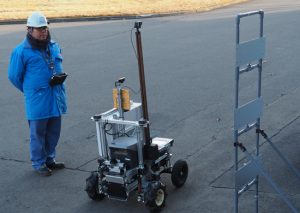
屋外自動点検デモ(Outdoor automated inspection demonstration)
In the indoor automatic inspection demonstration, the robot checked the surface temperature of the equipment with a thermal camera and read the values on digital and analog meters. It also detected abnormal sounds and anomalies.
When detecting anomalies, the AI determines what is different from the usual scenery.
The robot circles around the equipment and takes 360-degree videos with an omnidirectional camera. The captured videos are compared with videos of normal conditions to detect anomalies.
In the demonstration, the angle of the valve was deliberately changed, but it was detected immediately.
In the outdoor automatic inspection demonstration, the digital twin was used to control the robot’s movement and arms to inspect the equipment.
Using a digital twin makes robot operation much easier than with a radio-controlled robot.
With a radio-controlled robot, you have to give instructions like “go forward” or “go right” every time, which makes operation complicated, but with a digital twin, you just need to specify the destination on the screen and the robot will move there autonomously.
Managing Director Yamano said, “Because there are steps and other obstacles outdoors, using robots requires greater operability than indoors. There are many issues that need to be resolved, but we would like to continue to advance the automation of inspection and maintenance of outdoor equipment”.
※Translating Japanese articles into English with AI